High maintenance: How wind farms are maintained
High maintenance: How wind farms are maintained
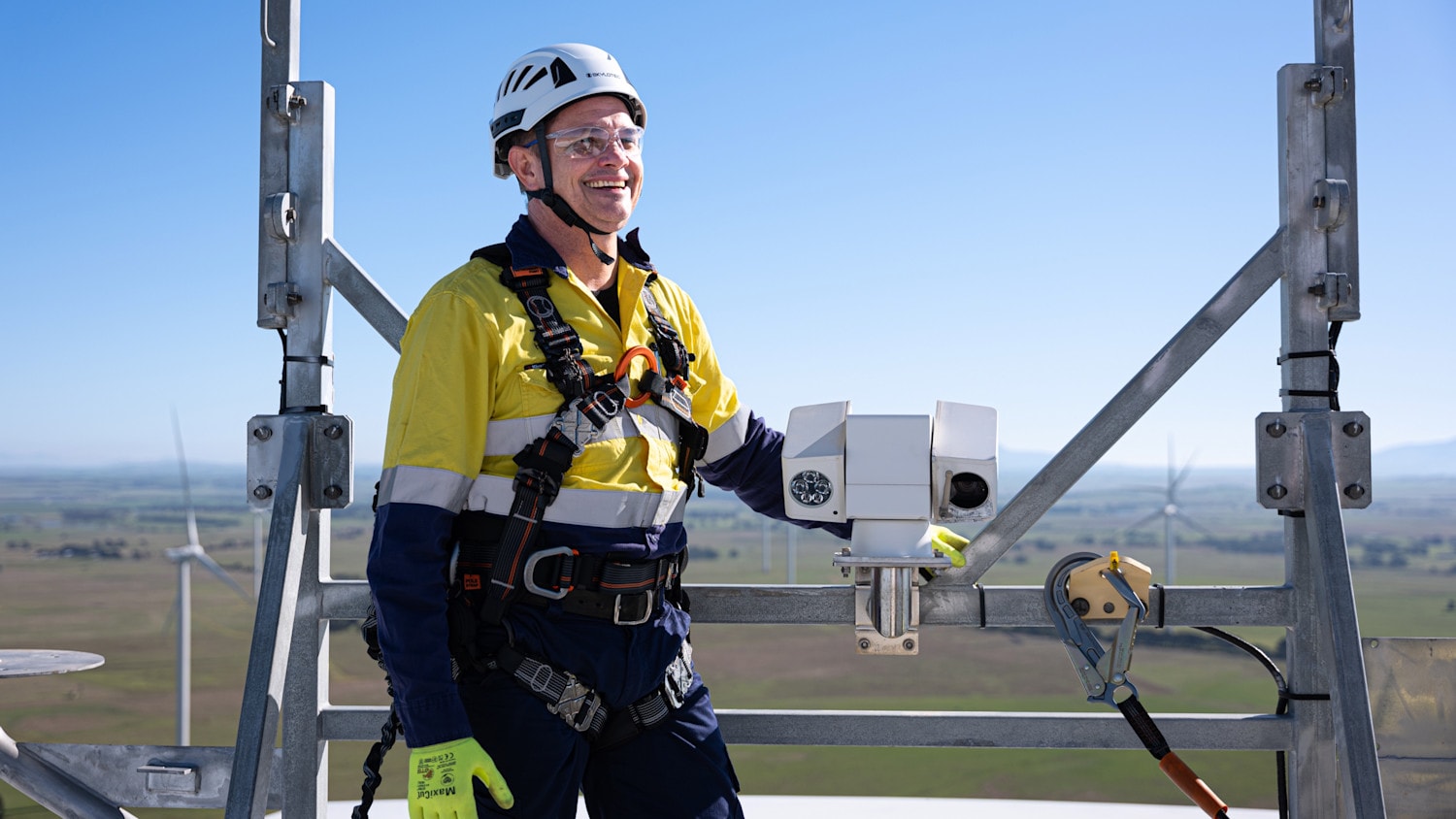
Queensland’s clean energy future depends on the efficiency of our wind farms. But what does it take to keep wind turbines running at peak performance?
More than 27 percent of Queensland’s energy supply already comes from renewables like wind and solar energy, and by 2035, that figure is expected to rise to 80 per cent. To reach that target, more than 2,000 new wind turbines will be needed.
Installing that many wind turbines is one thing– but keeping them running smoothly and efficiently is another. Here’s an inside look at what’s involved in wind farm maintenance.
The importance of wind farm maintenance
Wind turbines are sophisticated machines exposed to harsh environmental conditions. Like all complex technical systems, they require regular inspections, maintenance and repairs to maintain optimal performance.
Wind farms typically have a life cycle of around 25 to 30 years, and as long as they’re properly maintained, most turbines will remain highly efficient throughout that time. But they require consistent upkeep to prevent parts from wearing out, which can lead to reduced efficiency, lost revenue – and, ultimately, higher energy costs.
How often do wind turbines need maintenance?
Most wind turbines require maintenance at least once every six months, though the frequency can vary depending on factors such as the type of turbine, its age, location, and the amount of wind energy produced.
Horizontal axis wind turbines (HAWTs), which capture wind energy from any direction, typically require more maintenance than vertical axis wind turbines (VAWTs).
Wind turbines consist of four main parts: the base, tower, the nacelle and the rotor blades, or propeller. Inside the nacelle is the generator, gearbox, drive train, and brake assembly.
The most common maintenance tasks include:
Blade inspection and repair: Checking for cracks and damage caused by exposure to sunlight, extreme temperatures and corrosion.
Gearbox maintenance: Inspecting for wear and tear, as gearboxes can fail after prolonged use.
Generator checks: Ensuring generators are working correctly to prevent mechanical or electrical failures.
Bearing maintenance: Regularly checking and lubricating bearings to prevent damage.
Nacelle cleaning: Removing dust and debris to prevent health risks and ensure efficient operation
Rotor maintenance: Keeping the rotor free of vegetation that can cause damage
Wiring inspections: Checking for damage to prevent short circuits and fires.
Oil changes: Regularly changing oil to keep gears moving smoothly.
Regular maintenance checks, including system connections and parts lubrication, help to detect any issues early, preventing costly breakdowns and extending the lifespan of the turbines. This ensures the continued reliability of wind farms, keeping them running in peak condition and avoiding significant problems.
How are wind turbines maintained?
Wind turbines stand between 150 and 270 metres tall, so repairing or replacing heavy equipment is a challenging, risky task.
Wind turbine technicians, or ‘windtechs’, specialise in the installation, inspection, maintenance and operation of wind turbines – and they make the trek to the top of these towers on a regular basis.
While cable lifts in these towers are more commonplace now, windtechs are required to climb a series of ladders to reach the nacelles of older towers.
And it’s not just about getting themselves there – windtechs carry their tools to the top. Think hand tools like spanners and sockets, as well as larger, heavier gear like torque wrenches, power packs and replacement parts.
It’s a high-stakes environment where safety is paramount. Technicians adhere to strict safety protocols, including using harnesses connected to a fall arrest system similar to a seatbelt, which locks in place if a fall occurs.
Windtechs work in teams of two or three, ensuring no-one is left alone to lift equipment with a winch system. They also carry self-rescue kits with an emergency defibrillator, a rescue device, a stretcher, and a rescue rope that’s long enough to go all the way from the top of the turbine to the bottom and back again.
Once in the nacelle, the real work begins. Routine maintenance for a modern wind turbine takes about 40 hours per year, with non-routine tasks adding similar time. Repairs to gearboxes, rotor blades or the generator would typically require more downtime.
By adopting a proactive maintenance strategy, wind farm operators can not only optimise the frequency of upkeep, but also significantly reduce costs and downtime, guaranteeing the long-term reliability and efficiency of wind turbines and ensuring they can continue to contribute to our sustainable future.
Subscribe to our newsletter
STANWELL SPARK
Receive news from Stanwell to your email every quarter and learn more about how we are transforming energy generation.