A day in the life of a power station employee
A day in the life of a power station employee
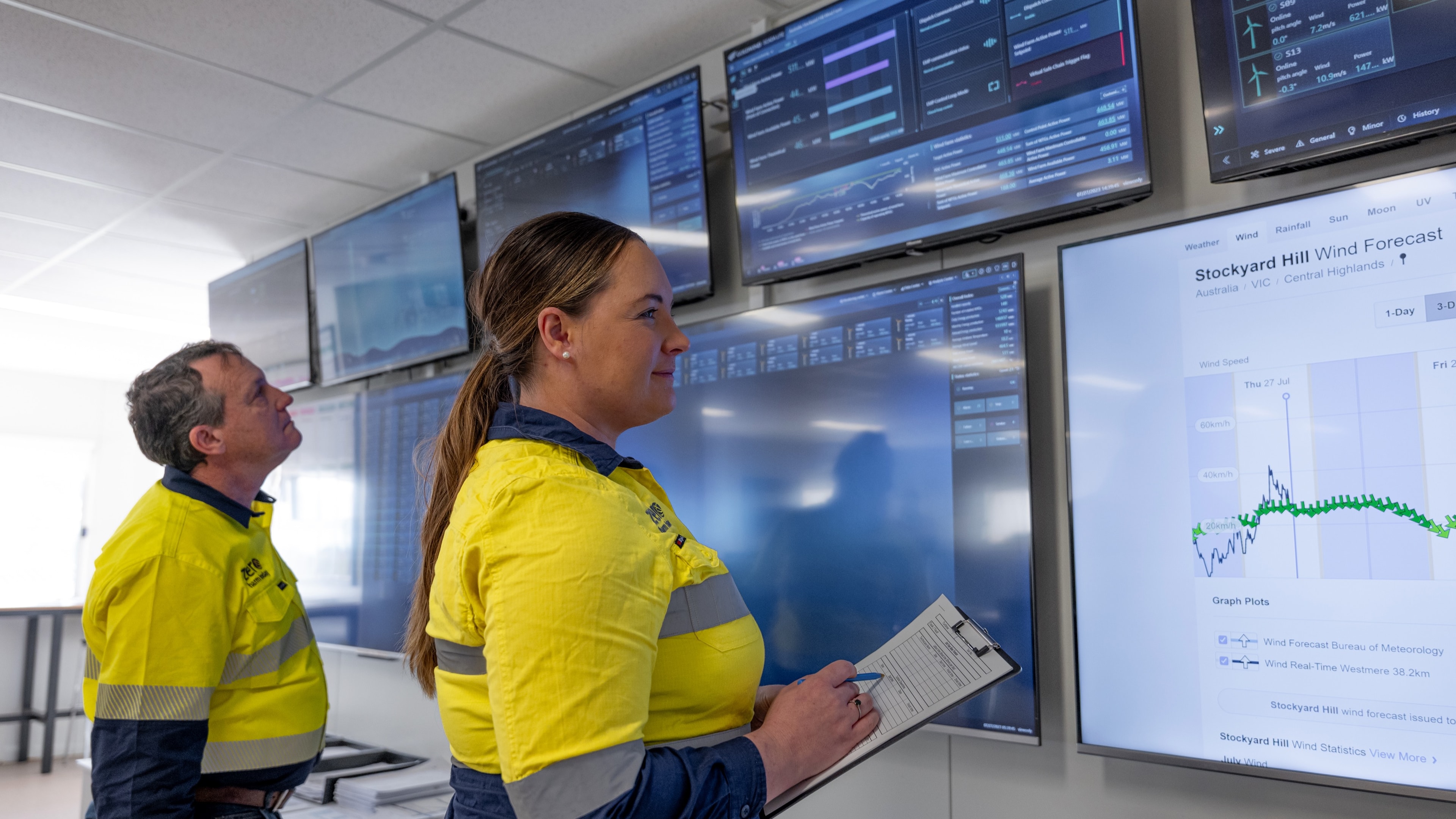
“In a nutshell,” Adrian Hill says, “my job is about capturing how we are finding better ways to do things.”
Adrian is the Optimisation Lead at Stanwell Power Station (SPS), a thermal power station located 23 kilometres south-west of Rockhampton.
Adrian is the first person to hold this role at the station. Before that, he was a Production Superintendent at the station for 11 years, and before that, he was contracted as a Project Manager for four years.
All up, he’s spent more than a decade and a half at SPS. It’s a turn of events he couldn’t have predicted when he was growing up in Brisbane.
“I never thought I’d be living in Rockhampton, to be honest,” he says. “But coming up here was more of a lifestyle choice than a career decision. It’s a fantastic place to raise kids – the private schools here are very reasonably priced, and the weather is great. I’ll just say we’ve got bags full of sweaters and jumpers we brought up with us that we’ve never had to use.”
Each morning, Adrian makes the 15-minute commute down the Capricorn Highway from his home in Rockhampton to SPS, where he goes about documenting the continuous improvements that are being made to the station and its processes.
“Stanwell was commissioned in 1992 and became fully operational in 1996, and it was at the absolute cutting edge of technology and design at the time,” he says. “It’s still one of the most efficient and economic traditional generation assets in Australia. But people are always finding better ways to do things, and it’s my job to help capture those improvements.
“We use a tool called JIRA to capture all of the ideas that people have, across five distinct categories – productivity, safety, environment, cultural and financial. That’s linked to Power BI, a reporting system that we use to track the impact of these improvements.”
Since Stanwell is a state-owned generator, improvements to the bottom line ultimately benefit taxpayers.
Adrian’s role sees him interacting with a vast swathe of SPS workers and stakeholders, and no two days are truly alike.
“I champion continuous improvement on site, and I spend a lot of time going around to the various production teams, educating them on the process and helping to set up reports aligned to their team,” he says.
“All ideas are good ideas, and it can come from anywhere. A lot of ideas come from workers on the floor, and from contractors, who are seeing this stuff up close every day and thinking about better and more efficient ways things can be done.
“Other improvements come from learnings from the Tarong power stations, which are also owned and operated by Stanwell, and from our industry partners. Sometimes they might come from other industries altogether. That’s why it’s important for me to visit other sites and build as wide a network as possible.
“Of course, there has to be a business case for some of these ideas, and due diligence has to be done before they’re implemented, but there have been a lot of improvements made this way. The trick is to make sure we capture them and monitor their impact. That’s why my job is to liaise with everybody, essentially, across all of the various departments, to be aware of the improvements and get them into our system.”
As an example of the impact these improvements can have, Adrian points to the decision to refurbish and repair diaphragms – parts of the steam turbines that power the station – rather than replacing them outright.
“Instead of spending $2 million replacing the diaphragms in the turbine, we can refurbish them during a planned outage and spend about $600,000,” he explains. “So, we’re saving well over $1 million there.
“That’s an extreme example, but sometimes it’s just about getting better deals – working with the teams across sites to buy parts in bulk, for instance, and saving money that way – and sometimes it’s about productivity initiatives that free us up to do other work.”
Adrian’s role also involves providing support for planned outages. Every generating unit in every power station in the National Electricity Market (NEM) is required by law to undergo a regular, scheduled maintenance overhaul. These planned outages are carefully coordinated ahead of time with the Australian Energy Market Operator (AEMO).
“During an outage, my day will usually start with a 6:45am pre-start meeting with the Outage Team and the Co-ordinators of the various areas at the power station,” Adrian says.
“Workers at power stations tend to be divided up into different strategy groups – you’ll have teams such as Material Handling, Boiler, Water & Chemical, Power Systems, Instrument & Control as well as Operations, to name a few. This meeting is a brief overview of today’s key events that can be passed on to each of their Teams at their morning pre-starts.
“At the 3pm outage meetings, the leaders of those teams provide updates on the progress of their particular area as well as any upcoming events. At these meetings, a summary of the Project progress is provided. This update is then communicated to the rest of the site to be presented for the next lot of pre-start meetings that night and the following morning.
“It’s very important that we have these updates and ensure that everything is on track each day, because a big focus of these outages is delivering the plant back online by the date that’s been arranged with AEMO.
“I also work with our procurement specialists, to ensure we stay on budget, and touch base with our training department to make sure they’ve got everything they need. On a normal day, we’d have about 200 people on-site, but during an outage, we peak at about 600 people. All of those extra workers need to do online training and inductions before they arrive, so I check in with the training team to ensure that’s all on track.
“We also have paramedics on-site 24 hours a day throughout the duration of the outage, which is managed by Site Health & Safety.”
Outages draw large numbers of workers from overseas and interstate to the region, so Adrian also works with local accommodation providers to ensure they have COVID management plans in place. He also liaises with Queensland Health to ensure that Stanwell is satisfying the current testing requirements and health directives.
“It’s an interesting time,” he says. “Every morning, I check to see if there are any new cases at the station, monitor when the active cases are due back, and make sure we have someone else in place with a similar skillset to cover their role if needed. It’s all about maintaining the continuity of the project.”
Finally, at the end of each day, Adrian checks all of the continuous improvement data that’s been added to Power BI that day.
“I just like to make sure that all of the data is accurate and adding value,” he says. “Because at the end of the day, that’s what this role is all about – adding value.”
Subscribe to our newsletter
STANWELL SPARK
Receive news from Stanwell to your email every quarter and learn more about how we are transforming energy generation.